High Pressure Die Casting
Effective HPDC (high-pressure die casting) can produce thousands of premium molded casts in a short amount of time while utilizing a single mold. This highly economical and cost-effective approach to high-pressure die casting mold design can produce casts with uniform quality and high degrees of accuracy. High-pressure die casting mold development provides premium quality, near “net shape” parts at a highly cost-effective price point.
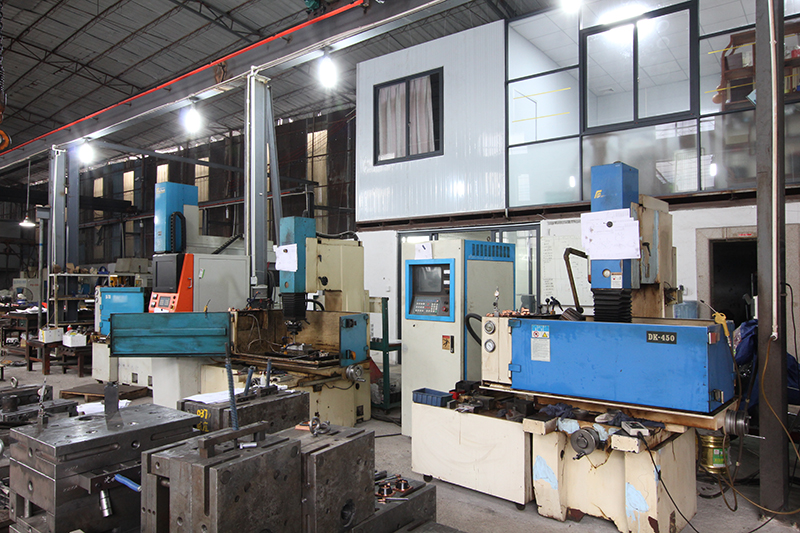
Looking for a premium high-pressure aluminum or zinc die casting mold manufacturer? Saint Rich is a custom designer, manufacturer, and supplier of premium high-pressure die casting molds to meet your project needs. Contact Saint Rich Die Casting or Request a Quote to complete your zinc or aluminum die casting mold today.
The Saint Rich Aluminum & Zinc High Pressure Die Casting Mold Manufacturing Advantage
When it comes to high-quality custom die casting mold development, several influences contribute to the overall success of the process. Saint Rich provides custom zinc and aluminum die casting mold production services to your project specifications. Saint Rich delivers the following die casting service advantages:
- First Class Engineering
- Die-cast tools designed in house
- Manage and oversee all aspects of tooling
- Developing injection process parameters: gate size, location, feeding speed, fill time, injection pressure, press size
- Parting line, runner, overflow, venting, cooling
- Minimum and Maximum wall thickness
- Choice of the mold material and hardness based on mold forces calculation
- Superior or Premium Grade H13, Uddeholm Orvar or Dievar
- Flow simulation
- Draft, radii, filets
- Establishing machining stock
- Utilization of both domestic and overseas tooling suppliers
High-Pressure Die Casting Molds Provide Superior Repeatability
Die casting molds from Saint Rich Die Casting and Machining utilizes aluminum and zinc alloys to produce small to large identical part run castings for your manufacturing needs. Die cast mold development is a versatile process that enables the production of a large quantity of small to medium-sized castings.
High Pressure Die Casting Design & Development Services
Saint Rich’s first-class team of in-house engineers can oversee all aspects of tooling and the injection process. We can produce thousands of high-quality molded casts in a short amount of time.
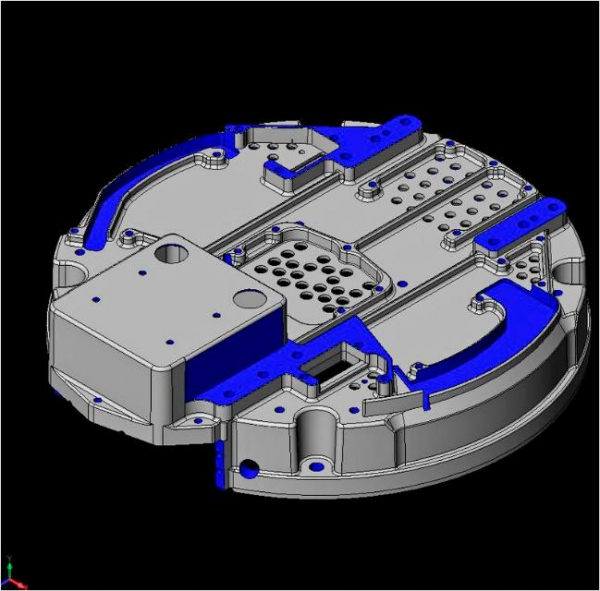
3D Rendition of casting converted from hog out configuration
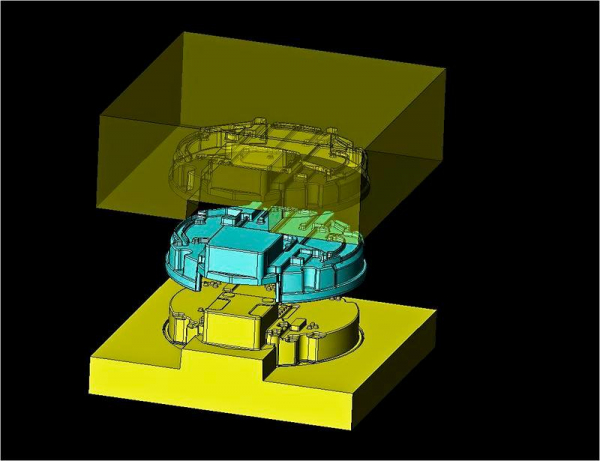
Computer graphic of die casting mold
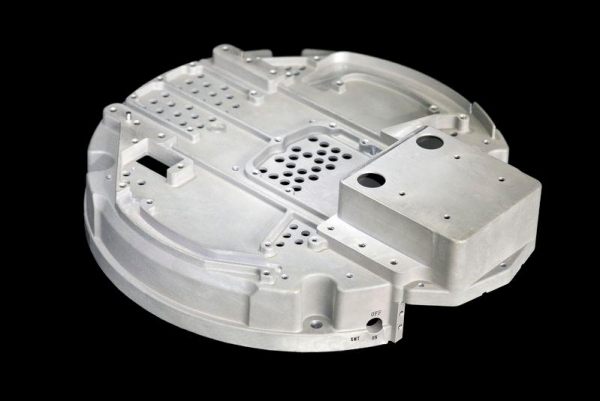
Aluminum alloy casting for aerospace industry
How are Die Casting Molds Manufactured?
Die casting is a manufacturing process commonly used to produce accurately dimensioned, sharply defined, smooth, or textured surface metal parts. It is accomplished by forcing molten metal under high pressure into reusable metal dies. The die casting mold manufacturing process follows the subsequent procedures regarding die cast mold manufacturing:
- A mold is created in at least two sections to allow the proper removal of the casting.
- The sections are mounted securely within the machine and are arranged so that one is stationary while the other is moveable.
- The two are tightly clamped together.
- Molten metal is injected into the die cavity, where it quickly solidifies.
- The die halves are drawn apart, and the casting is ejected.
Compared with sand or permanent mold processes, HPDC is the fastest method for producing exact non-ferrous metal parts.
How are High Pressure Die Casting Molds Constructed?
The molds utilized in the die casting mold design process are constructed from premium, heat-resistant steel grades. The molds are halved to form a cavity into which the liquid metal is pressed during the casting process. A die casting mold is so strong over a million parts can generally be created with a single mold. However, the actual life of the mold will solely depend on the die casting materials used.
Additional Considerations for Die Casting Mold Design
Some of the additional factors that should be considered before starting a die casting mold development project include the following:
- Gate calculation, feeding speed, and fill time
- Press size, clamping forces calculation
- Shot sleeve choice and calculation
- Venting and overflows
- Establishing cast and technological Datums
- Establishing machining stock
Die Casting Mold Development Benefits
Die casting utilizes non-ferrous metals (such as aluminum alloys or zinc alloys) to manufacture components. The chosen alloy for an application depends on budget, weight, and material properties. At SKS Die Casting, we can provide you with die cast molds that match your design specifications. Some of the advantages of HPDC molds include the following:
- Gate calculation, feeding speed, and fill time
- Press size, clamping forces calculation
- Shot sleeve choice and calculation
- Venting and overflows
- Establishing cast and technological Datums
- Establishing machining stock
Contact Saint Rich for High-Pressure Die Casting Production Services
In the market for zinc and aluminum die casting mold production services? We have you covered. SKS has been your premier manufacturing source for die casting mold development since 2007. Contact us at 86-18933357957 for more information or request a quote for specific pricing today.