How to Choose the Right Die Casting Manufacturer for Your Business
– A Guide for Procurement Professionals
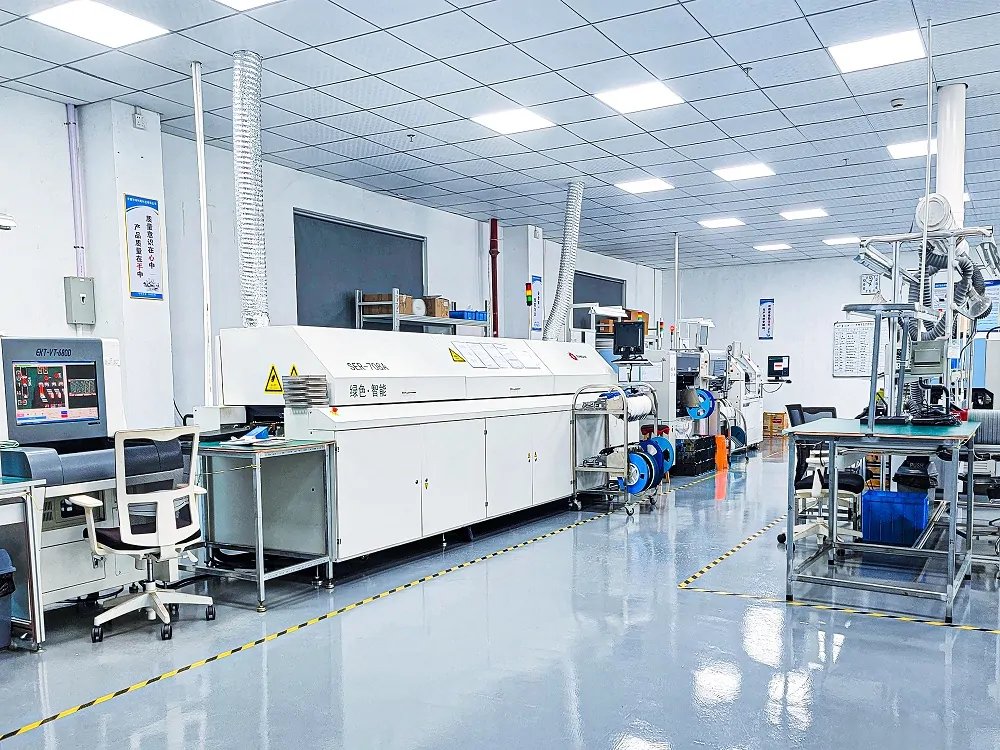
Introduction
Selecting the right die casting manufacturer is crucial for businesses looking to source high-quality, cost-effective components. Whether you need OEM die casting services for automotive, electronics, or industrial applications, choosing the right supplier ensures durability, precision, and supply chain efficiency.
In this guide, we’ll explore the key factors to consider when evaluating a die casting supplier, helping you make an informed decision and optimize your sourcing strategy.
Industry Experience & Specialization
When choosing a die casting company, industry experience plays a vital role in ensuring product quality and manufacturing efficiency.
✅ Proven Track Record: Look for manufacturers with 10+ years of experience in die casting production.
✅ Industry Focus: Some suppliers specialize in automotive die casting, while others focus on electronic enclosures or industrial machinery parts.
✅ Case Study: A European electronics company reduced product defects by 30% after switching to an experienced aluminum die casting supplier with advanced quality control.
Manufacturing Capabilities & Production Volume
Not all die casting manufacturers have the same production capacity. Choosing a supplier that meets your volume requirements ensures on-time delivery and cost efficiency.
🔹 High-Pressure vs. Low-Pressure Die Casting: Understand the difference based on your product needs.
🔹 Production Scale: Can the manufacturer handle low-volume prototypes and mass production?
🔹 Technology & Equipment: Advanced CNC machining and robotic automation enhance precision and reduce defects.
Example: A U.S. automotive brand cut costs by 15% by partnering with a best die casting manufacturer offering high-volume automated production.
Quality Control & Certifications
A reliable die casting supplier should adhere to strict quality standards and certifications.
🛠 ISO 9001 & IATF 16949: Ensures compliance with global automotive and industrial standards.
📊 X-Ray & CMM Inspections: Verifies internal defects, porosity, and dimensional accuracy.
🌍 RoHS & REACH Compliance: Essential for environmentally friendly die casting parts.
Tip: Always request a First Article Inspection (FAI) report before placing bulk orders.
Cost-Effectiveness & Pricing Structure
While pricing is a major factor, the lowest cost isn’t always the best choice. Consider these factors when evaluating cost:
💰 Mold & Tooling Costs: Ask about upfront mold investment and potential long-term savings.
⚖ Material Selection: Aluminum, zinc, and magnesium alloys impact both cost and durability.
🚛 Logistics & Shipping: Evaluate lead times, freight costs, and supply chain efficiency.
A global industrial manufacturer saved 20% in production costs by selecting a China-based die casting supplier with optimized material sourcing.
Customization & OEM Die Casting Services
For businesses requiring custom die casting parts, selecting a manufacturer with strong R&D and engineering support is critical.
🔹 CAD & DFM (Design for Manufacturability) Support: Reduces errors and optimizes designs.
🔹 Surface Finishing Options: Powder coating, anodizing, and plating enhance durability.
🔹 Prototype Development: Rapid prototyping allows quick validation before mass production.
Choosing an OEM die casting services provider ensures flexibility and design precision.
Supply Chain & Logistics Management
Efficient supply chain management guarantees on-time delivery and reduced production delays.
✅ Lead Time & Production Cycle: Evaluate the supplier’s average turnaround time.
✅ Global Distribution Capability: Ensure seamless shipping to Europe, the US, and other key markets.
✅ Risk Mitigation: Work with a reliable die casting supplier to prevent material shortages and delays.
Sustainability & Eco-Friendly Manufacturing
Sustainable practices are becoming increasingly important in die casting manufacturing.
🌱 Recycled Materials: Many best die casting manufacturers use 85%+ recycled aluminum.
⚙ Energy-Efficient Production: Advanced die casting machines consume 30% less energy.
♻ Eco-Friendly Finishes: RoHS-compliant coatings reduce environmental impact.
Choosing a sustainable die casting supplier not only meets regulatory requirements but also enhances brand reputation.
Conclusion
Selecting the right die casting manufacturer is a strategic decision that impacts product quality, cost-efficiency, and supply chain reliability. By considering experience, production capabilities, certifications, and sustainability, businesses can optimize their procurement process and build long-term supplier partnerships.
📩 Get a Free Quote & Sample Today!
Looking for a trusted die casting supplier? Saint Rich offers custom OEM die casting services with ISO-certified quality and global shipping.
📞 Contact us now for a free consultation & quotation!